When it comes to manufacturing iron gates, durability, aesthetic appeal, and efficiency are the top priorities. As a professional manufacturer of powder coating lines, Yantai clear have seen firsthand how an advanced coating system can revolutionize the production process. By integrating a specialized powder coating line, gate manufacturers can not only improve product quality but also increase their production speed and reduce waste. In this article, we’ll explore how upgrading to a high-performance powder coating line can transform iron gate production.
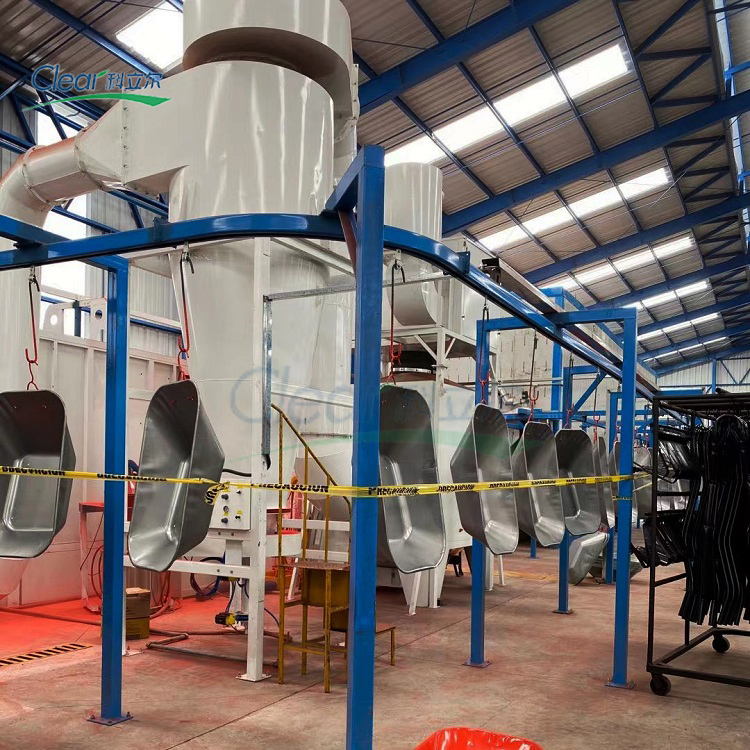
The Power of Powder Coating for Iron Gates
Iron gates are subject to harsh environmental conditions, from rain and snow to intense sunlight and extreme temperatures. To ensure longevity, gates need to be coated with a durable and protective finish. This is where powder coating comes into play.
Unlike traditional painting methods, powder coating is a dry finishing process that uses a finely ground powder. This powder is applied electrostatically to the metal surface and then cured in an oven, forming a hard, durable layer that is resistant to chipping, scratching, and fading. For iron gates, powder coating offers numerous benefits, including:
– Long-lasting protection against the elements.
– Aesthetic versatility, allowing for a range of colors and finishes.
– Environmentally friendly process with no solvents or VOCs.
– Enhanced corrosion resistance, especially for outdoor applications.
However, to maximize these benefits, the coating process must be precise and efficient. This is where a modern powder coating line comes into play.
How a Powder Coating Line Can Boost Production Efficiency
A well-designed powder coating line streamlines the entire coating process. From the preparation of the iron gates to the final curing stage, each step is automated for consistency and speed. Here’s how a dedicated powder coating line can improve efficiency:
1. Automation and Consistency:
With an automated powder coating line, the application of the powder is consistent, reducing the chances of human error. The electrostatic application ensures that the powder adheres evenly to every surface of the gate, even in hard-to-reach areas. This consistency not only results in a high-quality finish but also reduces the need for rework, saving both time and material costs.
2. Faster Production Cycles:
Powder coating lines are designed for high throughput. The system is optimized to handle multiple gates at once, significantly speeding up the production process. Since the coating is applied in a single pass, there’s no need for multiple layers or drying times, further shortening production cycles. This allows manufacturers to increase their output and meet demand more effectively.
3. Reduced Material Waste:
Traditional spray painting methods often result in overspray and wasted material. With a powder coating line, excess powder can be recycled and reused, minimizing waste and reducing costs. The precise control over the amount of powder applied ensures that the gates are coated evenly without excessive buildup, helping manufacturers stay within their material budget.
4. Improved Finish Quality:
Powder coating lines offer superior control over the coating process, resulting in a smoother, more uniform finish. This not only enhances the appearance of the iron gates but also improves their durability. The powder is baked onto the surface at high temperatures, creating a strong, durable bond that resists chipping and scratching. This ensures that gates maintain their look and functionality for years, even in the toughest conditions.
Customization and Flexibility
Another key advantage of using a powder coating line is the flexibility it offers in terms of customization. Whether you’re producing simple, functional gates or highly decorative ones, the coating line can be adjusted to meet your specific needs. You can choose from a wide range of colors, textures, and finishes to match the desired aesthetic. Whether you prefer a matte finish, gloss, or metallic sheen, powder coating allows for limitless creative possibilities.
Additionally, the curing ovens used in the powder coating process can be customized to handle different gate sizes and production volumes. This flexibility allows manufacturers to scale their operations without sacrificing quality or efficiency.
Cost Efficiency and ROI
While the initial investment in a powder coating line might seem substantial, the long-term benefits far outweigh the costs. The efficiency gained through automation, reduced material waste, and improved production speed leads to significant savings over time. Manufacturers can also expect a reduction in maintenance costs due to the durability of the coating, which helps reduce the need for repairs and replacements.
Moreover, the high-quality finish provided by powder coating can increase the market value of the finished gates, giving manufacturers a competitive edge in the market. Customers are willing to pay more for gates that are aesthetically pleasing and built to last, providing a strong return on investment for the manufacturer.
Conclusion
In today’s competitive market, it’s essential for iron gate manufacturers to maximize production efficiency while delivering high-quality products. Upgrading to an advanced powder coating line can significantly improve both the speed and quality of gate production. By automating the coating process, reducing waste, and ensuring a consistent, durable finish, a powder coating line helps manufacturers stay ahead of the competition while meeting customer demands for high-performance, aesthetically pleasing gates.
If you’re looking to boost the efficiency of your iron gate production, investing in a modern powder coating line could be the solution you need. With the right equipment, you can streamline your production process, reduce costs, and deliver superior products that will stand the test of time.
share this page