In modern industry, surface coating of metal components serves not only aesthetic purposes but also enhances their corrosion resistance, wear resistance, and other physical properties.
Here are several common surface coating processes and their specific applications:
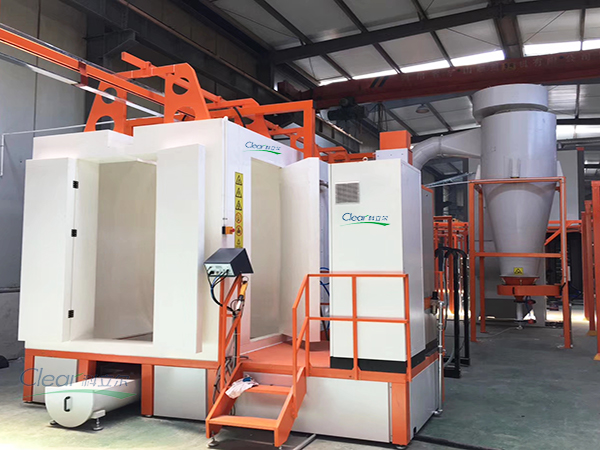
1. Electroplating
Introduction:Electroplating is the process of depositing metal ions onto a metal surface via electrolysis to form a uniform coating. Common metals used in electroplating include nickel, chromium, copper, and zinc.
Applications: Primarily used in automotive, electronics, and architectural decoration. For instance, automotive components such as wheels and door handles are often electroplated to enhance both appearance and corrosion resistance.
2.Spray Coating
Introduction:Spray coating involves evenly spraying liquid or powder coatings onto metal surfaces using a spray gun to create protective or decorative coatings.
Applications:Widely used in household appliances, furniture, automotive, and construction industries. For example, the shells of appliances like washing machines and microwaves are frequently coated using spray techniques for durability and aesthetics.
3. Anodizing
Introduction:Anodizing is an electrochemical process that enhances the corrosion resistance and surface hardness of aluminum and its alloys by forming a dense oxide layer on the surface.
Applications:Mainly utilized in aerospace, consumer electronics, and construction materials. For instance, the casings of smartphones and tablets often employ anodized aluminum to increase durability and modern appeal.
4. Chemical Deposition Coatings
Introduction:Chemical deposition involves depositing metal coatings on metal surfaces through chemical reactions. Common types include chemical nickel and copper deposition.
Applications:Widely used in electronics, electrical engineering, medical devices, and petrochemical industries. For example, chemical copper deposition is crucial in ensuring good conductivity and corrosion resistance in printed circuit boards (PCBs).
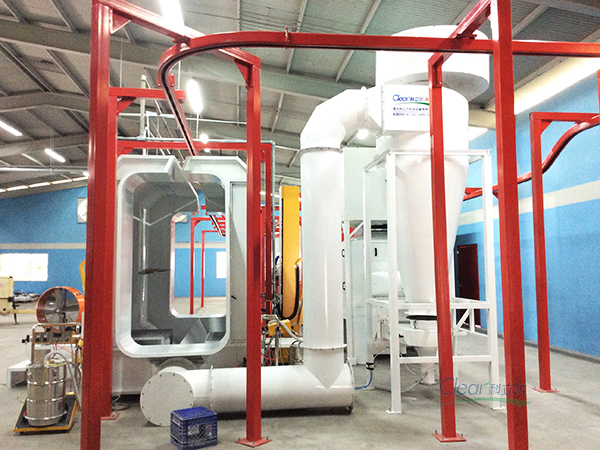
5. Thermal Spraying
Introduction:Thermal spraying is a technique where metal or ceramic materials are heated to melting point and then sprayed onto substrate surfaces to form coatings.
Applications:Primarily applied in aerospace, energy, and automotive industries. For instance, turbine blades in aerospace engines often utilize thermal spraying to enhance high-temperature and wear resistance properties.
6. Electrophoretic Coating
Introduction:Electrophoretic coating involves depositing charged paint particles uniformly onto metal surfaces under the influence of an electric field.
Applications:Widely used in automotive, household appliances, and industrial equipment. For example, automotive body parts are often electrophoretically coated to improve rust resistance and surface quality.
7. Sol-Gel Coatings
Introduction:Sol-gel processes convert sols (liquids) into gels (solids) to form uniform coatings on metal surfaces.
Applications:Mainly applied in optical lenses, high-temperature materials, and corrosion-resistant coatings. For instance, anti-reflective coatings on optical lenses are typically prepared using sol-gel processes to enhance optical performance and durability.
8. Chemical Conversion Coatings
Introduction:Chemical conversion coatings form a protective film on metal surfaces through chemical reactions.
Applications:Widely used in automotive, aerospace, and construction materials. For example, phosphating treatments on automotive bodies are common to enhance corrosion resistance and coating adhesion.
Conclusion:
These metal surface coating processes not only meet the diverse needs of different applications but also play a crucial role in enhancing product performance and extending service life. Selecting the appropriate coating process is essential for the successful application of products. We hope this article helps readers better understand and choose the most suitable surface coating technologies.